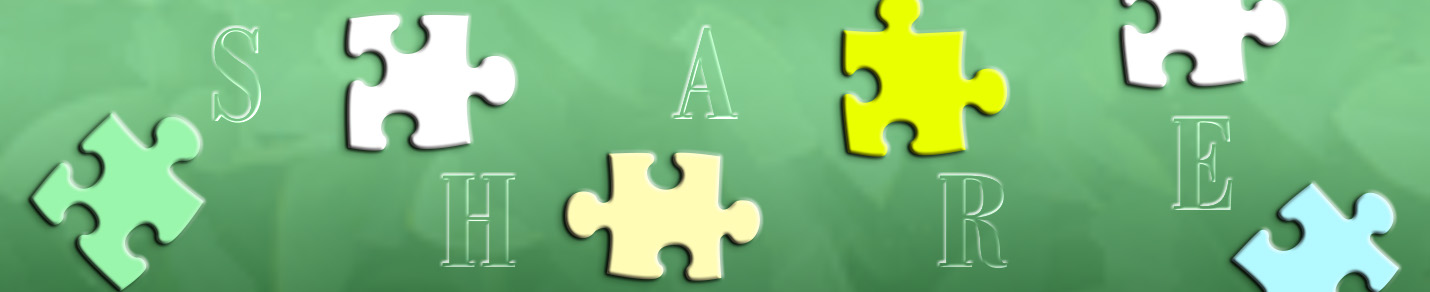
蒸汽系统设计八大问题
蒸汽系统设计效果既影响着项目投资额,也制约着生产运行能源利用效率,还关系到生产安全性、产品品质、生产效率、系统稳定和可靠性、系统长期运行成本等等。
这些年,尽管我国在蒸汽应用技术方面有了长足进步,但我们在广泛的市场调研中发现,蒸汽系统设计中存在的问题令人触目惊心!绝大多数企业的蒸汽系统存在设计问题,而且85%以上的蒸汽用户存在很严重问题。这些项目从设计之初就注定了热能浪费和效率偏低的必然性。
孚雷德根据市场调研了解到的情况,整理出蒸汽系统设计中常见的八个方面的问题,与大家分享如下:
管道口径 蒸汽系统管网涉及供汽总管、车间分管道、生产单元支管、用汽设备供汽管以及疏水管道和冷凝水回收管等。这些布置于室内外的管道蜿蜒曲折,纵横交错,总长度少则上千米,多则数万米。如此庞大的管网系统形成了一个散热面积巨大的散热器,其热能散失于周围环境。更严重的是,绝大部分管径都偏大,而且多数大过两个等级,让本来就很大的“散热器”面积又增加很多。比如,DN150管道比DN100的散热面积增加了50%左右。
蒸汽分配 蒸汽分配涉及总汽源到各用汽车间、车间分管到各生产单元以及用汽设备供汽管等各部分蒸汽分配和输送、管道布局和走向、取汽点位置以及管道连接方式等。如何在满足用汽要求的前提下,缩短管道总长度,降低管道压损,减少管网热损,实现蒸汽高效输送和分配,为用汽设备提供高品质蒸汽,是对蒸汽分配环节的要求。而现实情况是,蒸汽系统设计中,蒸汽分配混乱,管道重复冗余,管道走向不合理,取汽方式不正确,等等,问题普遍而严重。
蒸汽压力 蒸汽系统设计中的蒸汽压力问题主要有几个。第一,汽源过早减压后长距离低压送汽。这不仅对管道口径要求提高,而且降低了供汽侧的压力稳定性;第二,一种压力贯到底。这种总减压后以同一压力向设备终端供汽的方式,会导致有些设备存在高能低用而有些设备却有时因供汽压力不足影响生产的问题;第三,压力设定不合理。即使对设备用汽压力进行分组或单独设定,若压力设定值普遍偏高,也会影响热能利用效率。
蒸汽减温 对于汽源为过热蒸汽的场合,为了提高用汽设备效率和提升系统安全、稳定性以及延长设备寿命,有必要对过热蒸汽进行减温。在什么位置减温以及减温到什么温度,这是个容易被忽视却又很重要的问题。现场调研时经常发现,减温器的位置选择不合理,导致用汽端蒸汽品质较差。而且,减温系统出口温度设定不正确也是常见现象,这又会使得问题更加严重,造成用汽点蒸汽压力波动大和含水多等问题。
阀门口径 如上所述,蒸汽管道口径偏大的问题非常普遍,由此必然引发蒸汽阀门口径偏大的后果。阀门口径大,往往价格就高,而且阀门口径越大时对密封、关紧力和操作力度的要求都会更高,这些都必然反映到用户购买成本的增加。此外,管道和阀门口径的偏大又会驱使企业在生产过程中经常会对阀门进行部分开启,如此做法又会加剧阀芯和阀座局部磨损,造成阀门寿命缩短。对于自动控制阀,口径偏大产生的后果比起手动阀会更加严重。
梯级用能 欲提高蒸汽系统的热能利用效率,需要高能高用、温度对口、低能低用,必要时高带低融合使用。在设计中,最常见的高能低用现象就是高压蒸汽用于低压即可满足的设备上,这不仅造成热能浪费,也因提高了设备、管道的耐压耐温要求而增加投资;对于低品质的热能,比如低压闪蒸汽、工艺二次汽和低温水,直接用于加热温度要求较低的设备上是最佳选择。只有当低品质的蒸汽无法满足要求,才需考虑高带低的蒸汽提压。
凝水回收 在冷凝水回收环节的设计中,常见的问题包括疏水管口径和疏水阀选型错误、冷凝水支管和回收总管口径选择问题、管道走向不合理、凝水汇入点连接方式错误以及冷凝水回收方式不当等等。在实际设计中,疏水阀出口管道走向和布局问题比较严重,通常会造成疏水背压过大和水锤发生。此外,冷凝水直接汇集到开式水箱/槽是一种惯常设计方法,然而这种情形会有白汽外冒,既不利于节能降耗,又影响厂区环境。
余热利用 余热利用环节的设计需要解决余热怎样收集、用在哪、怎么用和如何高效用等几方面问题。蒸汽系统余热主要包括低压闪蒸汽、工艺二次汽、蒸汽凝结水等。目前,浪费比较大的是低压闪蒸汽和工艺二次汽的外排。有些企业,将闪蒸汽冷凝成热水后回收到循环水系统,此举不仅浪费热能,而且增大了循环冷却系统负载,造成二次浪费;大多数情况下,凝结水的回收利用往往限于对水的利用,而热能大部分损失了。
设计工作是蒸汽系统建造的前提和基础。优秀的设计方案不仅能为企业大幅降低建造投入,更是企业长期生产运行中提质增效、节能减排的必要条件。所以,很大程度上,效益是设计出来的。反之,低水平的设计不啻会增加企业短期投资,而且会导致企业长期的能源浪费和生产效率低下。因此,可以讲,浪费始于设计。